Robotic Welding Cell
Introduction
Robotic Welding Cell demonstrates a flexible manufacturing cell meaning it has an inventory of its own, material handling system, variety of parts with dynamic-order.This welding cell can be a part of production line and act as standalone system.Use of single or multiple robots may involve use of a PLC also.This cell uses a saftey PLC.This cell has all these features and the basis of selection can be done in a way that the cell will be programmed, utilization of peripheral devices (proximity sensors, pneumatic cylinders), safety devices and Automatic Identification & Data Capturing (AIDC) devices like RFID, vision camera etc.
The cell has following level of flexibility but the decision can be made on the basis of the flexibility required as per the following parameters:
1. Variety of parts for simultaneous production
The cell has following level of flexibility but the decision can be made on the basis of the flexibility required as per the following parameters:
1. Variety of parts for simultaneous production
2. Change of schedule
3. Ready for new part
Workstations and layout design :
Workstations in the cell are as per the following given applications and subject to following parameters :
1. Load/Unload stations for the cell: It is the area where the raw materials are incepted in/out of the cell.
2. Inventory storage area: An inventory storage where the storage of the raw material is kept.
3. Inspection area: An area where the material post operations are inspected for quality. This is kept as a separate unit away from the cell but it can be an integral part of the cell itself.
4. Operations area: An area where the operations like welding is performed. In the cell , this area is more of a workspace since two robots are responsible for performing welding on the material. And it can be anywhere in the robot's workspace.
5. Layout design: It is an integral part before identifying the robots and environment preparation and also plays a key role in safety of the cell.
CAD Design & Simulation:
The 3D visualization and detailing of the cell is done using a designing software. The robotic path simulation software asists in defining the best possible, collision free environment that is going to be the basis of the layout design and all other hardware that are going to be installed in the cell. Apart from designing & fabrication of the cell it helps in performing the robot simulations to generate offline program, collision free environment (this is how the level of flexibility achieved) for robots at operating stage and generating Augmented Reality applications.
3. Ready for new part
Workstations and layout design :
Workstations in the cell are as per the following given applications and subject to following parameters :
1. Load/Unload stations for the cell: It is the area where the raw materials are incepted in/out of the cell.
2. Inventory storage area: An inventory storage where the storage of the raw material is kept.
3. Inspection area: An area where the material post operations are inspected for quality. This is kept as a separate unit away from the cell but it can be an integral part of the cell itself.
4. Operations area: An area where the operations like welding is performed. In the cell , this area is more of a workspace since two robots are responsible for performing welding on the material. And it can be anywhere in the robot's workspace.
5. Layout design: It is an integral part before identifying the robots and environment preparation and also plays a key role in safety of the cell.
CAD Design & Simulation:
The 3D visualization and detailing of the cell is done using a designing software. The robotic path simulation software asists in defining the best possible, collision free environment that is going to be the basis of the layout design and all other hardware that are going to be installed in the cell. Apart from designing & fabrication of the cell it helps in performing the robot simulations to generate offline program, collision free environment (this is how the level of flexibility achieved) for robots at operating stage and generating Augmented Reality applications.
Physical System
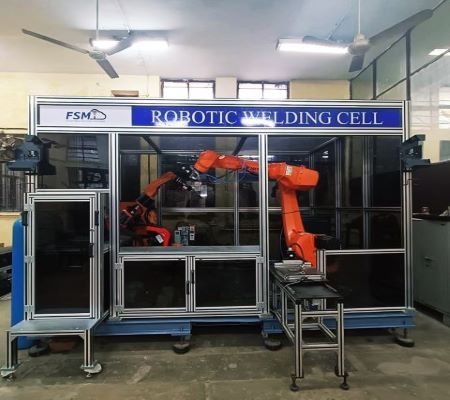
CAD View
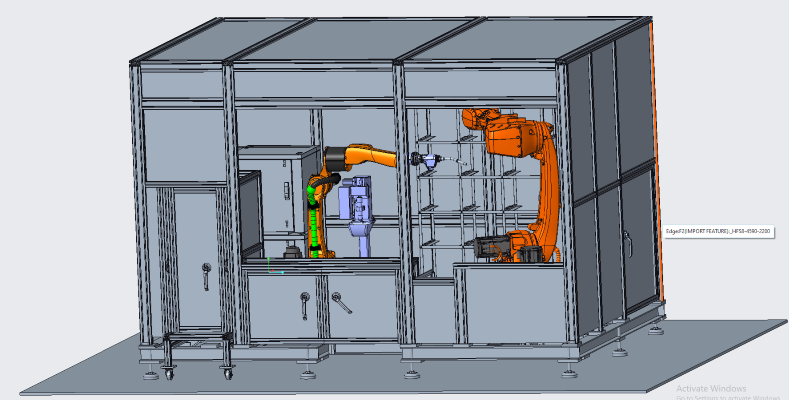
Video Description
The cell programming can be done in atleast two ways. Online programming where teach pendant is used and other is offline programming where the simulation is done in a separate software like RoboDK and KUKA Sim4. This helps in visualising and performing collision free path generation for both the robots. The video below demonstrates the offline programming method where we can see two robots performing indexed type motion. The offline programming helps in virtual commissioning and without impacting the production.
Indexed motion using RoboDK-1
Indexed motion using RoboDK-2
Services
Simulation & Testing
Job work & research
Prototyping
Customer Order Proessing
Site Integration
Machine-as-a-service
Contact us today for implementing
"Smart Manufacturing"
Call us for any query
011-26582053, 8076197190