Smart Lathe Machine
The Smart Lathe Machine project exemplifies the transformation of a legacy, manually operated lathe into a smart machine. Widely used in the Indian metal-cutting industry, the goal of this project is not to convert the lathe into a CNC machine, but to capture comprehensive process parameters and machine state data, providing real-time visibility while maintaining minimal disruption to the operator.
An array of sensors has been installed to monitor critical parameters, including:
Feed Rate and Depth of Cut: Measured using a 2-axis digital readout.
Spindle Speed and Gearbox Temperature: Captured by dedicated sensors.
Machine State: Indicated by a tower light.
In addition, a safety interlock with the chuck key ensures the machine cannot start with the key left in the chuck, enhancing operational safety.
The collected data is transmitted through a Programmable Logic Controller (PLC) via an industrial communication protocol, enabling real-time monitoring.
Machine Learning Models for Smart Manufacturing
Leveraging the data captured from the smart lathe, two machine learning models have been developed to enhance predictive capabilities:
Surface Roughness Prediction Model (Ra): This model predicts the surface roughness of turned components.
Remaining Useful Life Prediction Model (RUL): It estimates the remaining useful life of the cutting tool in minutes, based on energy characteristics and 3-axis vibration data from the tool post.
These advancements showcase how legacy machinery can be retrofitted with smart technology to deliver valuable insights and predictive maintenance capabilities, advancing smart manufacturing processes.
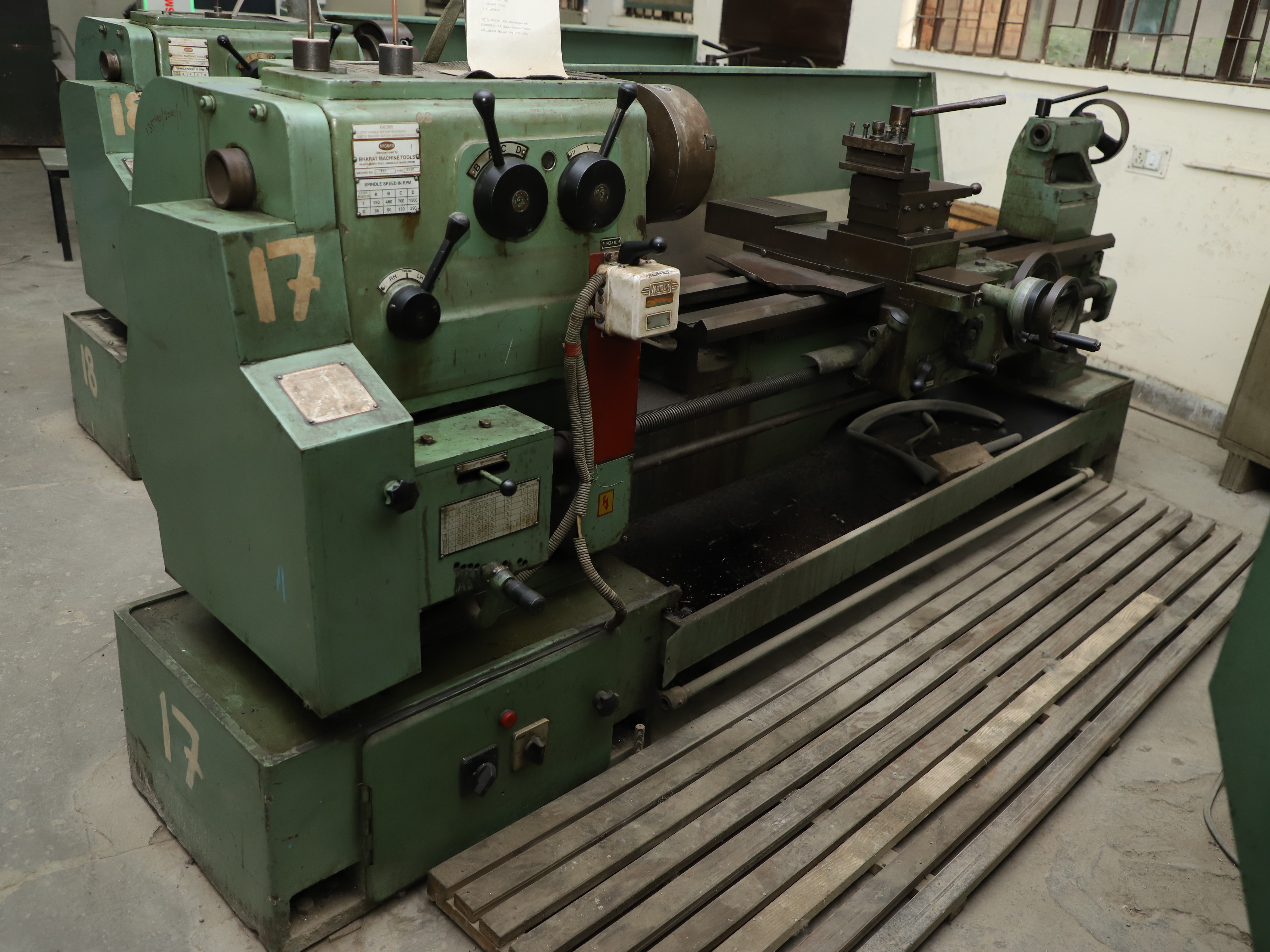
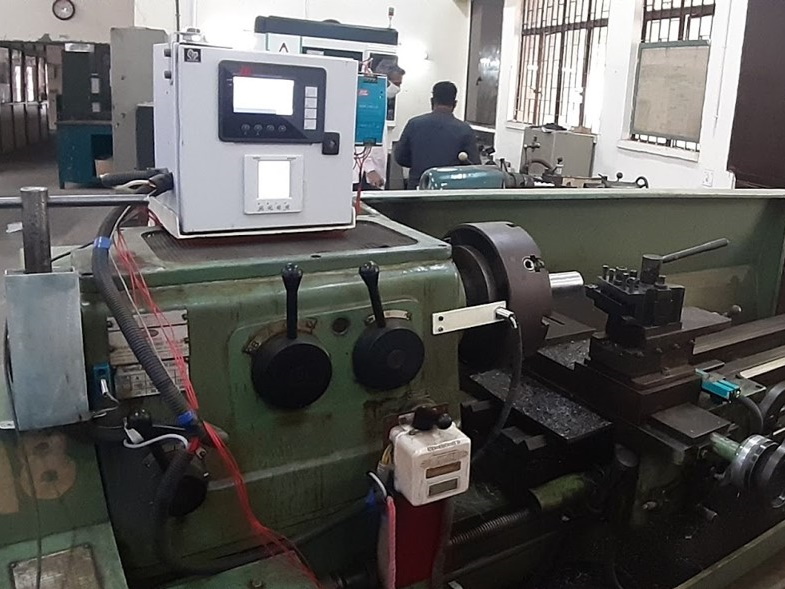
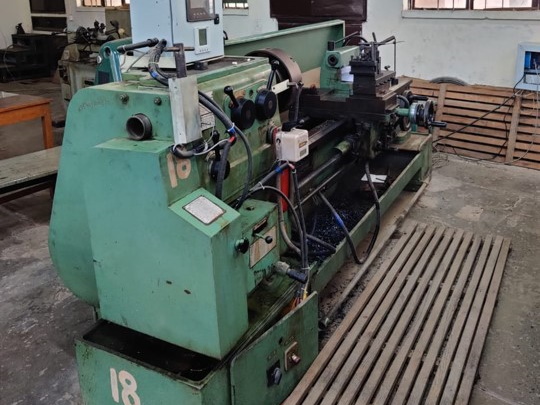